Silicon Carbide Tubes丨Improved Corrosion Resistance for Heat Exchangers
Silicon carbide tubes are prized for their outstanding hardness, thermal conductivity, and resistance to wear, corrosion and thermal shock. These silicon carbide tubes have outstanding performance in severe environments.
Reaction Bonded Silicon Carbide Tube RBSiC Tube
They’re ideal for extreme environments such as heat exchangers, industrial furnaces and chemical processing. Their light weight construction matched with exceptional mechanical strength guarantees efficiency and durability even in the most corrosive environments.
With the addition of silicon carbide tubes, industries not only see enhanced performance but significant savings in maintenance costs for mission-critical operations.
What Is a Silicon Carbide Tube?
ATCERA silicon carbide tubes are next-generation advanced ceramic materials built to withstand high-temperature and abrasive industrial environments. These tubes are specifically designed for use in environments demanding superior resistance to high temperatures, mechanical stress and corrosive conditions.
Silicon carbide’s remarkable physical, chemical, and electronic properties have made them critical components across multiple industries. From semiconductors to petrochemicals, these materials thrive in the most demanding environments. In addition to their excellent thermal performance, silicon carbide tubes are extremely reliable.
They are at their best under extreme conditions, acting as structural members, crucibles, or heat exchanger tubing.
Composition of Silicon Carbide Tube
The microstructure of silicon carbide tubes plays a major role in their performance. These tubes are manufactured from silicon carbide, which is a compound that consists of silicon and carbon. By bonding these materials in various methods, we are able to improve desired attributes of the tubes.
Oxide-bonded silicon carbide tubes are extremely corrosion resistant, which allows them to transport the most aggressive of chemicals. For even greater mechanical strength, especially in high-stress applications, nitride-bonded alternatives are available.
East Side’s carbon-bonded variants provide exceptional thermal properties, such as high conductivity and thermal shock resistance. Silicon carbide tubes provide amazing versatility with different types of bonding. That lets us design them to suit the unique requirements different industrial applications have.
The Role of Silicon Carbide in Harsh Environments
Silicon carbide’s unique physical and chemical properties make it the ideal material for demanding, extreme conditions. Capable of withstanding temperatures reaching 4,500°F, these tubes are ideal for any application that requires exposure to extreme high heat. Their extreme hardness, similar to that of diamond, guarantees abrasive wear resistance, even in the most changeable conditions.
Corrosion Resistance
Silicon carbide tubing shows extraordinary corrosion resistance. This extraordinary resiliency allows them to function dependably in sectors that manage aggressive acids, alkalis, and oxidizers.
Their low coefficient of thermal expansion combined with their high thermal conductivity makes for outstanding thermal shock resistance. This provides robust durability, including during extreme thermal cycling.
Silicon carbide tube is exceedingly popular in mission critical applications. They shine in the semiconductor sector, auto parts, and mechanical seals.
Background on Shell and Tube Heat Exchangers
Silicon carbide shell and tube heat exchangers are an essential part of industrial operations providing efficient heat exchange between fluids. In addition, these systems are very flexible and have high thermal efficiency.That’s why they enjoy broad use across the chemical processing, power generation and petrochemical industries. Yet, their performance is in many cases limited by the difficulties associated with the management of corrosive media.Extreme chemicals and extreme heat can break down traditional materials, resulting in constant maintenance and costly downtime.
Identifying the Challenge
When using traditional materials in heat exchangers, companies can incur millions of dollars losses each year. It is estimated these losses amount to $500,000, primarily due to particle wear and erosion.
This problem is compounded by the frequent repair and replacement required, which interrupts operations and drives up expenses. The significant downtime resulting from these issues highlights the need for more durable materials such as silicon carbide tube.
These tubes reduce wear and increase resistance to extreme environments. Therefore, they save you more than just maintenance costs by increasing the lifespan of your equipment.
Challenges of Managing Corrosive Substances:
Insights on Silicon Carbide Tube
The performance of tubing is critical to efficient heat exchanger operation. This component is key to efficient heat transfer. The tubing in these systems passively transfers heat between two fluids. It reduces energy loss during this conversion process to a minimum. Traditional materials can combat corrosive media. This shortcoming can lead to operational difficulties and increase costs.
Challenges of Corrosive Media
Corrosive media such as acidic or caustic chemicals can quickly eat away at conventional materials. Stainless steel and copper alloys are especially at risk for this kind of damage. Over time, these materials corrode the tubing. They undercut the walls and form defects that damage the heat exchanger’s performance.
In the chemical processing industries, hydrochloric acid and sulfuric acid are often aggressive enough to eat through common materials in short order. This puts equipment at risk of leaks and even catastrophic failures. This corrosion compromises the structural integrity of the tubing which eventually leads to a quantifiable drop in thermal performance.
Roughened surfaces change the flow dynamics of the fluid, creating turbulence that can severely differ heat transfer performance. Consequently, energy use increases to maintain temperatures within acceptable ranges. Additionally, constant malfunctions and upkeep cause more operating hours to be wasted on maintenance, cutting away potential productivity.
In certain industries, such as power plants or a refinery, continuous operation is imperative. These challenges pose a clear, direct threat to profitability and reliability.
Limitations of Existing Solutions
To fight back against corrosion, most industries would reach for titanium, nickel alloys or some kind of coated steel. Though these materials provide excellent resistance to chemical degradation, they have significant shortcomings. Titanium, for instance, has exceptional resistance to a wide range of corrosive media but is cost prohibitive for most large-scale applications.
Nickel alloys do offer moderate durability, but are very susceptible to stress corrosion cracking in the right (wrong) environment. Coated steel provides the most economical initial cost. Even so, it is prone to coating delamination or pinhole defects, which allow corrosive media to penetrate and corrode the base material.
The inherent trade-offs in cost, durability and performance underscore the reality that legacy solutions won’t cut it. As a result, demand for materials that can resist corrosion is skyrocketing. These materials need to retain their mechanical and thermal properties through a large temperature and pressure range.
Of these, silicon carbide tubing emerges as the clear best alternative. It’s unique mix of corrosion resistance and high thermal conductivity makes it the perfect solution for addressing these challenges.
Analysis of the Enhanced Wear Resistance of Silicon Carbide Tube: A Threefold Improvement
Silicon carbide tubes have proven indispensable in today’s most advanced heat exchanger technology. They offer unparalleled performance advances over conventional materials. This, combined with the superior wear resistance of silicon carbide, makes them a critical component in high pressure, high temperature industrial settings. This post focuses on their benefits, wear resistance properties, and practical uses in the field.
Silicon carbide (SiC) tube, as shown above, is made for extreme high-performance, high-wear applications. They have a remarkable hardness of 9.5 on the Mohs scale, exceeding that of tungsten carbide, which is rated at 8.5-9. This remarkable hardness translates to outstanding scratch resistance and performance in abrasive environments.
SiC tubes have very high thermal conductivity and low thermal expansion. Their great chemical stability allows them to be used in heat exchangers. In heat exchanger applications, SiC tubes survive and thrive in conditions where other materials have perished. Because of these properties, for example, silicon carbide tube can be used for handling aggressive chemicals or salt-laden solutions.
These tubes survive and thrive in high-temperature processes. They lead in industries such as petrochemical refining or metal melting, where temperatures frequently exceed 1,800°F. Their high density and low porosity further optimize their structural integrity and long-term performance under even the most extreme conditions.
Wear Resistance Analysis of Silicon Carbide Tube
Silicon carbide tubes have 3x the wear resistance of steel. In reality, they exceed tungsten carbide’s wear resistance by over three times. Experimental data has repeatedly shown that their extreme hardness and chemical stability result in this superiority.
SiC’s high Young’s modulus (stiffness) guarantees resistance to deformation and, therefore, to surface degradation during abrasive occurring under working conditions. For instance, in industrial grinding systems SiC tubes resist particle erosion up to 3x better than the other available options.
In addition, their low porosity reduces the ingress of corrosive elements, avoiding surface wear and extending the service life of components. In industries such as chemical processing, abrasive slurries present a great danger with continual use. These slurries can rapidly erode any material that is not sufficiently robust.
With their unique combination of hardness, chemical stability, and structural density, silicon carbide tubes provide a strong solution to the challenges of high-wear environments.
Application Scenario Case Studies
Industries have gradually turned to SiC tubes for their superior ability to prevent costly wear-related problems. In the petrochemical industry, for instance, they are deployed in heat exchangers to process corrosive gases and liquids.
In one impressive example, a refinery used SiC materials to replace conventional metal tubes. The move resulted in a stunning 40% decrease in maintenance costs in just three years. In abrasive slurry transport pipelines, SiC tubes have proved to be 3x wear resistant. This results in continuous operation and increases the life of the equipment.
The real-world benefits of SiC tubes go beyond just saving money. This increased wear resistance results in less frequent shutdowns, greater efficiency of the system overall, and a lesser environmental impact due to lower material waste.
This combination of benefits is helping to make SiC tubes the material of choice in a wide range of high wear, high temperature applications.
Key Advantages of Silicon Carbide Tubes
These silicon carbide tubes are a revolutionary engineering material, and especially for shell and tube configurations in heat exchangers. With their unmatched combination of features, they provide an advanced and trusted solution across industries that need strong, energy-efficient, high-performing materials.
Here’s a closer look at their benefits and how they stand up to extreme operational conditions.
Reduction in Equipment Downtime
Silicon carbide tubes provide excellent wear resistance. This remarkable property serves to dramatically increase the service life of equipment. Wear resistance silicon carbide also has a wear resistance over 30 times higher than that of carbon steel pipes.
This remarkable toughness protects against elemental wear in the most highly abrasive conditions. In chemical processing plants, solid particulate often suspends in fluid stream flows. The tubes’ excellent hardness, rated 13 on the Moh’s scale, ensures that their structural integrity lasts over long periods.
The economic repercussions of this durability are profound. Lower wear means less need for replacement and less shutdown time for maintenance. As an example, if a plant typically experiences five unscheduled downtimes per year due to component wear, just by replacing with silicon carbide tube, it would allow them to cut that number in half or more.
This change can save them thousands in lost operational hours and repair expenditures. Over five years, these savings can amount to over $100,000. This underscores the material’s tremendous importance in industrial applications.
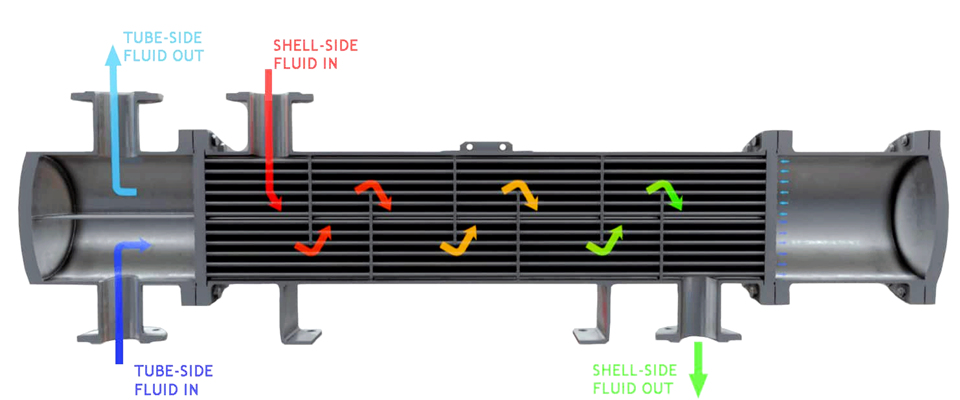
Lower Maintenance Costs
Widely recognized for their durability, silicon carbide tubes are known for reducing maintenance requirements. Combined with their excellent corrosion resistance, their strength under duress makes them a powerful option for handling harsh chemical environments.
They resist strong acids, alkalis, and hydrofluoric acid with ease. This resistance angers the repair advocates by reducing the frequency of repair dramatically. It makes repair work easier since the product can withstand chemicals that typically eat away at standard piping.
Their lightweight but mechanically robust construction make for easy handling in the field during installation and regular maintenance inspections. Silicon carbide tube has exceptional thermal shock resistance, with a ΔT of 1,100 °F.
This unique ability enables them to resist extreme temperature shifts without shattering or warping, greatly reducing the likelihood of failure. Over the long term, this resilience leads to a dramatic lowering of repair costs. Additionally, it allows companies to better focus their time and money on more mission-critical activities, increasing overall operational efficiency.
Comprehensive Benefit Assessment
The benefits of switching to silicon carbide tube is substantial. Less downtime, lower maintenance costs, and better efficiency are just a few of the advantages. These advantages combined have rendered them a must-have component of shell and tube heat exchangers.
Their very low thermal expansion, combined with high thermal conductivity (120-200 W/m·°F), ensure the best possible thermal performance. With a ceramic content greater than 95%, they have excellent structural integrity.
When combined with industrial systems that leverage these tubes, companies can realize improved cost savings, productivity gains, and an overall reduction in threat and operational risk.
Choosing Silicon Carbide Tube for Your Applications
Today, industries turn to silicon carbide tube because of their long-lasting durability and high performance. These tubes are ideally suited for use in heat exchangers and other extreme environments. Their extraordinary properties render them a powerful and trustworthy choice. Knowing their financial and operational advantages are key to making an informed decision.This section explores the key factors to help Operations Supervisors and Equipment Managers select the right silicon carbide tube for their projects.
Decision-Making Factors
When choosing heat exchanger tubing, Operations Supervisors and Equipment Managers need to weigh a few key aspects. These consist of thermal conductivity, chemical corrosion resistance, mechanical strength, and cost-effective nature. Silicon carbide tubes are uniquely suited for these applications because of their strong material characteristics.
Their high thermal conductivity ensures efficient heat transfer. This characteristic is unique and highly sought-after in industries such as petrochemical and metal melting, where temperature management is of utmost importance. Silicon carbide has the highest level of chemical resistance. This allows it to excel in extreme environments from corrosive chemical processes to high-temperature applications without failing.
Mechanical strength is another critical factor, especially when service requirements include exposure to high pressure or mechanical loading. Traditional metal tubing can struggle in the face of such circumstances and countless replacements or repairs can result. Silicon carbide tubing is capable of withstanding the harshest of environments.
This unique capability helps to maximize uptime and keep things running smoothly. From a cost perspective, the long-term savings achieved through durability, reduced maintenance, and operational stability often outweigh the initial investment.
Recommendation Rationale
When you need to improve equipment performance across the board, silicon carbide tube is the answer. Their high thermal efficiency leads to quicker heat exchange, the ability to move production processes and energy savings. Less energy consumption means lower energy bills.
It’s more than just helping DOD meet its sustainability goals and becoming better stewards of the resources they have. Because of their extreme hardness, these tubes reduce expensive maintenance cycles. In chemical processing applications, the use of wear- and corrosion-resistant materials results in a lower frequency of tube replacement.
That saves precious time and lowers labor costs. Their longer lifespan only increases that value, making them an economically prudent option for any operations looking to go the distance. By integrating silicon carbide tube, businesses can increase their systems’ reliability.
This innovation not only avoids the potential for unplanned shutdowns, which is important for any industry, but is absolutely critical for those industries that rely on continuous output.
Engage with Us Today!
Operations Supervisors and Equipment Managers alike should consider the unique benefits silicon carbide tubes have to provide. To learn more, contact ATCERA directly. Or come see us online to find out more about how our silicon carbide tubes can address your unique industrial applications.